Posted by Darren Pay on Nov 18, 2020
As an employer, you must ensure the safety of your employees from mechanical or non-mechanical injuries caused at the workplace. When operating any machinery, there is always a risk of getting injuries like bruises, burns, and cuts, or even fatal ones such as laceration, amputation, fractures, etc.
The purpose of a barrier is to avoid any workplace accidents and to protect the health of your employees. Therefore, it is essential to use guards at all times and to get a replacement as soon as possible if your existing one is inefficient.
Machine Injury Statistics
As per the OSHA statistics, 18,000+ equipment operators get injured every year, and around 800+ operators die due to accidents caused by unprotected machinery. If you do not use a machine barrier, not only are you going against the government standards set to protect employee health, but you are also endangering your employee.
Using an inefficient machine barrier or not using one at all exposes your workers to life-threatening injuries. If you notice that your existing barrier isn't protecting your workers, you should get a replacement to avoid any future incidents.
How to be Compliant with OSHA Standards
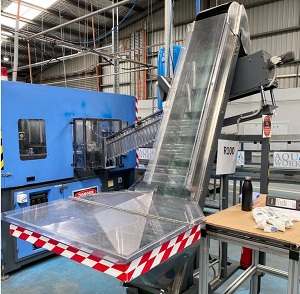
To be compliant with the OSHA standards, your machine barrier has to fit certain criteria. The guard should act as a barrier between the equipment and the employees, preventing the employee from entering or touching the point of operation.
It should be securely fitted and tamper-proof. It shouldn't delay, obstruct, or interfere with the employees work as the employee may try to detach the barrier if it does interfere with the operation of the equipment.
Lubrication and maintenance of the equipment should be possible even with the barrier attached and it shouldn't create any new additional dangers such as unfinished surfaces or shear points. If your existing barrier doesn't comply with these points, then you should consider a replacement.
Different Types of Equipment Barriers
There are a variety of machine barriers available for every type of equipment and different purposes. The two categories are fixed perimeter guards and point guards. A perimeter guard is a type of static protection that is installed in a specific area to prevent employees from accessing the machinery.
Often they are installed where robots or automated equipment operate. Whereas, guards fall into the point guard category, where its purpose is to act like a physical shield that protects employees from direct contact. There are a variety of safety devices that can be additionally used such as the electrical interlocks that instantly turns off the machine if any access point is unlocked, to prevent any injuries from occurring.
In a nutshell, following government standards and using barriers will not only save you from any legal issues, but it will also protect your employee from any injury and prevent any workplace accidents.